1. Project Overview
This project intends to build a 30 tons/day liquid waste +10 tons/day solid waste hazardous waste incineration device for Jining Wansheng Environmental Protection Materials Co., LTD., which is used for incineration and treatment of hazardous waste produced by the factory.
The industrial waste treated by this set of incinerator is mainly solid and liquid waste. The technical scheme includes a set of 30 tons/day liquid waste +10 tons/day solid waste hazardous waste incinerator acquisition, installation and commissioning part. The project location is in Jining, Shandong Province. This project intends to build an incinerator with a daily processing capacity of 40 tons and its supporting waste feeding facilities, flue gas treatment system, ash removal system, automatic control system, interlocking alarm system, waste heat recovery system, emergency discharge, tail gas treatment, etc.
No.
|
Name
|
Capacity
|
Thermal transfer value
|
1
|
Solid
|
420kg/h
|
3000 ~ 4000Kcal/kg
|
2
|
Liquid
|
1250kg/h
|
7000 Kcal/kg
|
Note: this incinerator can not be used for incineration of waste with flame retardant substances, high halide, high salt content.
1.1 Incinerator technical requirement
No.
|
Item
|
Unit
|
Specification
|
Remark
|
1
|
Average hourly incineration liquid waste
|
Kg
|
≥1250
|
|
2
|
Average hourly incineration solid waste
|
Kg
|
≥420
|
|
3
|
Rotary kiln outlet temperature
|
℃
|
850-900
|
|
4
|
Secondary chamber outlet temperature
|
℃
|
≥1100
|
|
5
|
Secondary chamber smoke residence time
|
s
|
≥2
|
100% load
|
6
|
Flue gas carbon monoxide concentration
|
mg/m3
|
≤100
|
1-hour mean
|
≤80
|
24-hour mean
|
7
|
Incineration efficiency
|
%
|
≥99.9
|
|
8
|
Incineration removal rate
|
%
|
≥99.99
|
Persistent organic pollutants ≥ 99.9999
|
9
|
Thermal reduction rate of incineration residue
|
%
|
<5
|
100% load
|
10
|
Daily capacity
|
ton
|
40
|
|
11
|
Annual running time
|
day
|
≥300
|
|
12
|
Oxygen content of flue gas at the the secondary chamber outlet
|
%
|
6-10
|
Dry flue gas
|
13
|
Heat conduction oil furnace outlet flue gas temperature
|
℃
|
300±25
|
|
14
|
Bag inlet and outlet temperature difference
|
℃
|
≤10
|
|
15
|
Velocity of filtering
|
m/min
|
0.4-0.6
|
Normal operation
|
16
|
Annual running time
|
h
|
≥7200
|
|
17
|
Overall engineering system availability
|
%
|
100
|
|
18
|
Range of load variation
|
%
|
70-110
|
|
2.1 Plant process description
Automatic delivery system——automatic feeding system——rotary kiln (separate kiln tail cover)——secondary chamber——SNCR denitrification system——Waste heat conduction oil boiler——quench deacidification tower——dry spray tower——bag dust collector——induced draft fan——SCR system——spray washing tower——packing tower——Wet electrostatic dust removal——chimney
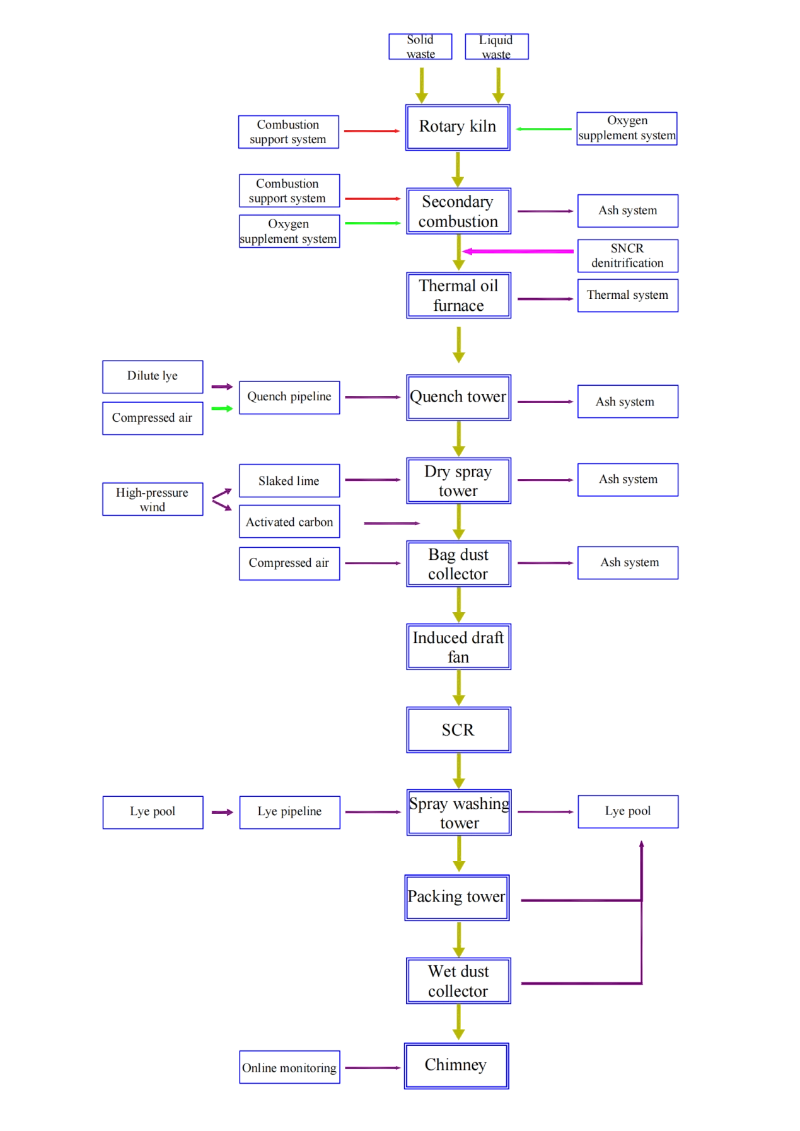
2.2 Brief description of the main process
The operator first opens the fan and purges the residual gas in the system. Then start the secondary natural gas burner, the natural gas burner attached to the primary combustion chamber, when the quench tower inlet reaches about 150℃ open the washing and spray pump, and the temperature in the kiln rises to about 800℃, the combustible hazardous waste is sent into the rotary kiln through the automatic feeding system and the automatic feeding system. The waste in the kiln is dried, pyrolyzed and incinerated under the combustion-supporting of the auxiliary fuel and the action of air disturbance. The total residence time of the waste in the kiln is 0.5 ~ 1.0h, and the whole combustion process is in a negative pressure state.
The flue gas generated after the primary combustion enters the secondary combustion, while the waste liquid is sprayed into the secondary combustion chamber or rotary kiln through the waste liquid spray gun, the secondary combustion chamber is actually a gas combustion furnace, and the unburned long and short chain hydrocarbons and CO and other flammable gases in the flue gas after the primary combustion are further turbulent mixing under the secondary wind, and can be fully burned in the "3T+E" environment to make dioxins decompose completely. Under normal circumstances, the furnace temperature in the secondary combustion chamber is above 1100℃, and the design total residence time is ≥2S. The organic hazards in the flue gas are completely destroyed and transformed into CO2, SOX and HCl gases to achieve the purpose of thorough sterilization, disinfection and deodorization.
The high temperature flue gas fully burned by the secondary combustion chamber directly enters the waste heat utilization system (waste heat conduction oil reheater) to cool down to about 280℃, and the inlet position of the heat conduction oil furnace is provided with the SNCR denitrification system (denitrification in the furnace) interface to remove nitrogen oxides. The flue gas from the heat transfer oil furnace then enters the quenching deacidification tower, where the lye is sprayed, the temperature is reduced to about 200℃ within 1 second, and the dioxins are prevented from being produced again, and then the lime and activated carbon are sprayed into the dry jet tower to remove acid gases such as HCl, SO2, HF and remove heavy metals and dioxins in the flue gas. Then the flue gas enters the bag dust collector to remove fly ash, waste activated carbon and other particles.
The flue gas from the cloth bag is introduced into the SCR denitration system by the induced draft fan to further remove nitrogen and oxygen compounds. The purified flue gas enters the two-stage spray tower to further purify the acid components and dust, and then removes the dust by wet electrostatic dust removal. The gas after reaching the standard is discharged at high altitude through the chimney.
Reviews
There are no reviews yet.